Taking action to reduce plastic waste
By using creativity and persistence, the packaging department team at Yamagata, Japan, managed to reduce their waste plastic material by 11 per cent, making them an inspiration for all sites globally. And it all started with one small idea.
Boehringer Ingelheim’s Yamagata site – 400 kilometers north of Tokyo – is surrounded by beautiful nature. On her daily drive to work, Yuko Goto, who works in the Yamagata packaging department, sees both the snow-covered Mount Gassan on the horizon and the many cherry fields that the Yamagata prefecture is famous for. “I feel very close to nature here,” says Yuko, “I am happy to live and work in such a beautiful environment.”

In the packaging department, Yuko and her colleagues ensure the steady supply of 45 different Boehringer Ingelheim products for customers and patients in Japan. Yamagata has started bulk export to regional markets such as Australia and New Zealand since 2023, and her team is also responsible for packing for export. When packaging medicines in an automatic process, scrap waste is created as the margin of the plastic film is cut away. Today, the Yamagata site produces 2 billion tablets a year — a process that also leads to 16 tons of waste plastic material.
Working close to the production line, the amount of scrap waste produced became evident to Yuko – and something she decided to change. In 2021, Yuko therefore submitted a proposal to re-evaluate the established production process to reduce material loss and to improve packaging efficiency.
“It was just sad to see all the material scrap waste. We had to act”, Yuko explains. At Yamagata, employees are encouraged to submit their own ideas for small “quick-win” projects, called “Kaizen” — an approach that has led to a continuous flow of proposals. “I have two children, and it is important to me to pass on a better future to the next generation”, Yuko shares.
Using our resources in a sustainable way
The approach in Japan is true for all of us at Boehringer Ingelheim and a great example of what we aim for. Our Leitbild states that “we feel responsible for our communities and are respectful of our resources”. Boehringer Ingelheim will always strive to be better: develop better therapies, enable better health care solutions, and contribute to a better world for future generations. This includes protecting natural resources and reducing waste. Our available natural resources are not endless, and to use them sustainably, the amount extracted needs to reflect the resource's capacity to recuperate and regrow.
“Our societies are currently using more resources than we have”, says Anthony Matheri, senior manager for circular economy at Boehringer Ingelheim. “According to the Global Footprint Network, already in May, countries like Germany or Japan have used more resources than one earth can sustainably support." Boehringer Ingelheim is aiming to do its part to reduce the global over-usage of resources. Through our global MORE GREEN program and by applying a holistic approach, we are working to reduce our environmental footprint, including in areas such as carbon emissions, energy, water, and waste.
Circular Economy helps us to keep resources in a loop
The concept of circularity – one component of which is waste reduction — promotes moving away from a linear business model of take-make-dispose. Instead, the approach encourages a circular business model that “closes the loop”, i.e., keeping resources in a “circular loop” where material is recycled and reused for as long as possible, or where the usage of raw material is reduced altogether. “One way that BI is increasing circularity within its operations is eco-design and green chemistry.” Anthony adds, “This means to challenge the status quo and consider product sustainability throughout the product life cycle of end-to-end value chain.”
That was a key learning for the Japanese team. The machine manufacturer claimed that it was impossible to change the established processes. But the team did not want to give up. So, instead they started innovating on their own and found a way to reduce material loss and to improve the packaging efficiency of 3 blister machines. They successfully reduced scraps for plastic film connection by half. This resulted in reducing waste of 100 meters of film per process order.
Through re-evaluating their processes, the Yamagata team managed to shorten the width of plastic film by 2 mm, leading to another reduction of 1.8 tons of waste. This also meant the scrap waste was reduced by 11 per cent. “There were many challenges, but in the end, we found a way to reduce the width of the plastic film and optimize the packaging material.” Yuko states with a smile on her face.
In addition to the reduced amount of waste, the weight reduction of the packaging materials has led to unexpected benefits. For example, logistics have become more efficient and employees’ safety has increased, since less volume means less weight that workers need to handle in connection with transfer.
Reducing plastic waste further
This project, which started as one small idea, has now snowballed to create new projects, which reduce plastic waste even further. The Yamagata site is also currently consulting with the machine manufacturer, to assess how they can collaborate to reduce packaging scrap waste further – or altogether. In addition, as the blister machine manufacturer has the highest market share in Japan, our initiative opens the possibility for many other clients to implement the changes as well — benefiting not only our company but also the whole of society.
So, how can a project that reduces the plastic film by 2 millimeters in Japan help us decrease our environmental impact globally?
“No one can be an expert in all areas.” Anthony Matheri points out, “but by bringing together our global community, we can help and inspire each other.” Key to this is building systems of knowledge exchange between different cross-functional teams around the world. In this way, we are sharing the experiences gained from local circularity projects and using them to initiate and scale up similar projects at other sites.
Anthony summarizes: “The waste reduction project in Japan has the potential to not only increase the circularity of BI’s operations locally, but also inspire many more similar waste reduction projects at BI sites around the globe.”
Every kilo helps and everyone can contribute when it comes to waste reduction. “Small things can make a huge difference”, Yuko agrees and tells us about how the project has given her the confidence that she can do more for the future. “I questioned what I took for granted, and realized the importance of breaking down stereotypes, and continuing to challenge myself. To contribute to a big change, I learned to find small opportunities and take action.”
Infobox
Plastic pollution – small particles with a long-lasting impact.
To reduce plastic pollution, action matters. This is what the World Environment Day 2023, led by the United Nations Environment Programme (UNEP), emphasizes.
Plastic pollution poses a critical challenge within circularity. Plastic is not biodegradable. This means that instead of decomposing, plastics break down into smaller pieces and even smaller pieces — so called micro- or nano plastics. These tiny plastic pieces have a devastating effect on the health of flora and fauna, impact our waterways and oceans, etc. negatively impact the health of both humans and animals. Boehringer Ingelheim is working on sustainable optimization solutions in line with the work of the UNEP, striving for a healthier future for humans, animals and the environment
Related Content
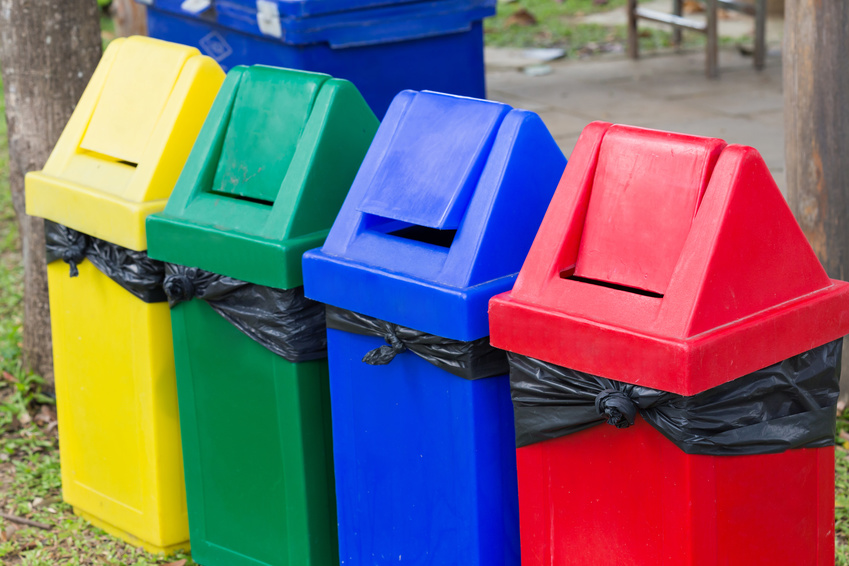
Waste
